Subscribe To Our Weekly Newsletter
Categories
From simple software updates to preparing for full machine automation, our TECSight team is here to cover all bases. We caught up with Integrated Solutions Manager Hamish Ross to talk about all things technology and Precision Ag.
Just like our customers, there’s been little rest for the TECSight team as harvest has rolled right into sowing this year. But for Integrated Solutions Manager Hamish Ross, the upcoming winter break will be the perfect time to catch up on all things data management.
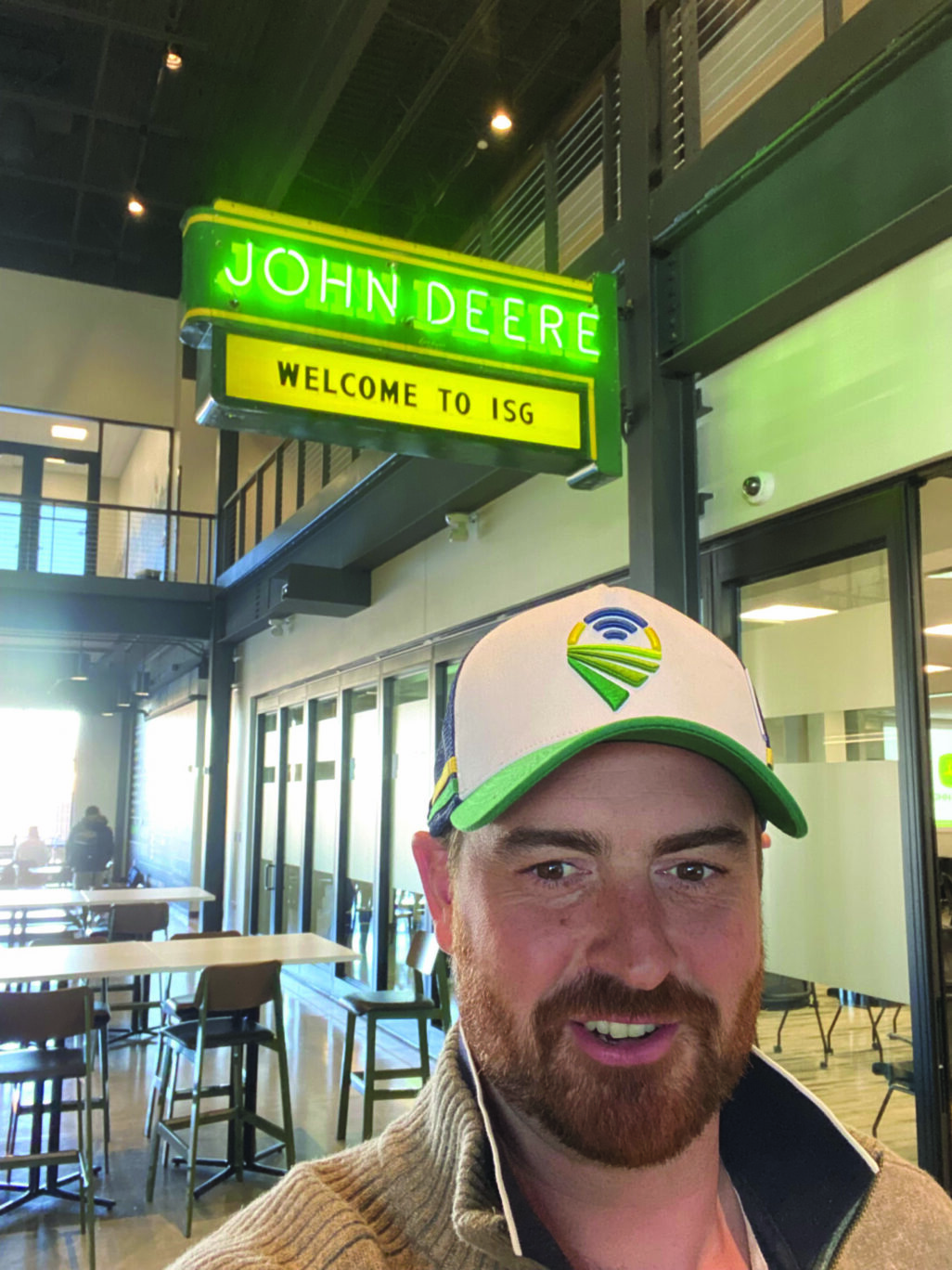
“Here at TECSight, we’ve been flat out with harvest finishing late due to the rain seeing not much of a reprieve in the January/February period.
“Our Remote Support team has kept up answering plenty of phone calls which have now steered into seeding and cotton pick and, given that we’ve sold a number of new pickers, our Field Services team have been getting out in front of our customers, sharing information and optimizing machines to make sure our customers are getting the most out of their purchase.
“They’ve also been running customer clinics focused on the new pickers because there's quite a few changes to them this year. This usually involves a walk-around of the machine to point out the key features and maintenance points and a bit of time in a classroom setting to run through the onboard technology and the data management side of things. We hope to do more of those customer clinics with other machines now that COVID restrictions have eased."Hamish Ross- Intergrated Solutions Manager
When it comes to data setup and management, and now that the crop is in the ground, now is the perfect time to get set up for spraying and spreading and Hamish said that more and more people are keen to know exactly how they can get the most out of their machine.
“We are busy helping customers make sure their machine is sending the data correctly and that it’s recording correctly so they can make data-driven decisions. In particular, James Niemeyer up in Dubbo has been getting out on-farm and really trying to grow that engagement within the customer group.
“I think people are hungry to learn more about Precision Ag because we’ve had a couple of really good years following tougher years. Farmers do what they need to in tough years, but now we’re seeing decent years with good yields and good commodity prices, they have the opportunity to think about the future of their operation and put steps in place to capture quality data so they can make those good, data-driven decisions into the future. Not to mention that input prices are challenging gross margin performance, so it’s really important to improve the per hectare efficiency.”
Road to Automation
For many farmers, John Deere’s announcement of its first-ever fully autonomous tractor ready for large-scale production has got them thinking about how automation will play a role in their farm operations.
“The key to having an autonomous tractor on-farm is a solid foundation, and that foundation is all about set-up. You have to have Operations Center setup and ready to go with things like accurate boundaries and making sure the naming conventions of all your fields and farms are right. It’s certainly worth investing time and money now getting these foundational aspects right to prepare for the future. Our Precision Ag services team is ready to get out in the field and delve into our customers’ Operations Center.
“One strong step forward is that Operation Center will soon be able to sync with Generation 4 displays, which will mean that boundaries, field names and guidance tracks will soon be able to sync across your fleet of machines. We’re really looking forward to that because it will eliminate some of the challenges operators have and we’ll be all geared up to help customers should they need support the day John Deere makes that announcement. There is a fair bit of preparation required but the efficiencies gained will be easily measurable.”
App Enhancements
John Deere is enhancing both Work Planner and the Operation Center mobile app to make things easier for farmers. For Hamish, one of the big recent improvements is Operations Centre adding more attributes you can edit.
“Now, you can jump in at end of seeding and make sure the documentation is correct for each field. If there’s a mistake, you can edit it, which is really important. Then, no matter what the operator puts in the picker or combine for a variety, it picks up that variety that’s logged in Operation Center.
“The same thing goes for boundaries. If you’ve got your Operation Center nice and neat and all your boundaries are correct, the data can be geo-located. So, the machine’s setup may say paddock A, but Operations Centre will put it in as paddock B because that’s what’s been entered. It’s a triple check, which is really handy if you have new operators in the machine.
“We know that from April to May it’s all systems go to get the crop in the ground and it’s quite easy that mistakes are overlooked in the hustle and bustle of sowing season. So it’s great that when there’s some downtime you can get in and edit things and make sure it’s quality data in/quality data out.”
Constant improvements to Work Planner are also making it easier for farmers to send an exact layout of the operation they want done to a machine and taking the guess work out of it for operators.
“With Work Planner, it doesn’t matter who’s in the machine, they just hit go and it pre-populates the operation cutting down the margin for error. It’s very easy to use, which is by design. There’s no point having incredibly complicated or hard to use programs in a time poor industry.
“Labour is such an important issue, so farmers have to be able to do it on the fly. John Deere has been great at recognizing that and providing products that are easy to use and it makes a farmer’s job a hell of a lot easier. It makes our job a lot easier, too, as we’re able to run customers through how to use it and they pick it up fast.”
If you’re on the path to automation and want advice on how to prepare, or just want to know how to get the most out of your machine right now, reach out to TECSight – call (02) 5924 5111.
Articles And Resources From The Hutcheon & Pearce Newsroom
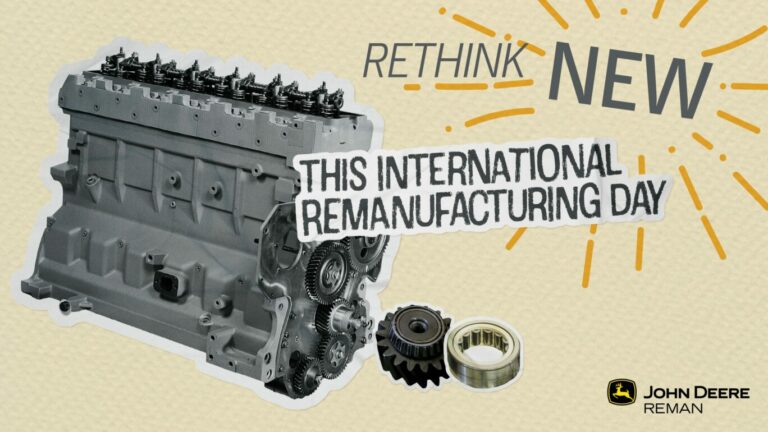
Embrace Sustainability: Discover the Impact of John Deere Reman Parts on Global Reman Day 2024
Embrace Sustainability: Discover the Impact of John Deere Reman Parts